A construction site is like a living organism. When all parts are in the right place, at the right time and performing well, it is buzzing with energy and progress.
But all that can come to a standstill rapidly. It takes just one key piece of equipment failing, an order of materials not being delivered on time, a crew not showing up, a storm coming in…
Managing all these risks on one site is hard enough, but for construction companies with many dozens of sites, it becomes a difficult and costly affair.
Just having raw data is not enough
Data was long seen as the solution to these problems. Collecting all the data from your workforce, your supply chain, your assets and deploying digital tools to monitor, manage and report on them should be the answer, right?
Over the past years we learned that this is not enough to optimize performance and run smooth operations. Let’s zoom in on assets as an example.
Just one piece of machinery generates up to 100,000 data records through IoT devices, sensors, or manual tracking. Multiply that by all your equipment on all your sites, and you end up with mountains of raw data.
Making sense of it requires cleansing, transforming, and organizing. It also needs connecting all your data sources to your existing workflow and operational systems, and its historical data.
And once that’s done, the real unlocking of the value can start; transforming the data into information that frontline workers can act on. Of course, that would require the information to be shared in real-time… Yet another hurdle many companies experience.
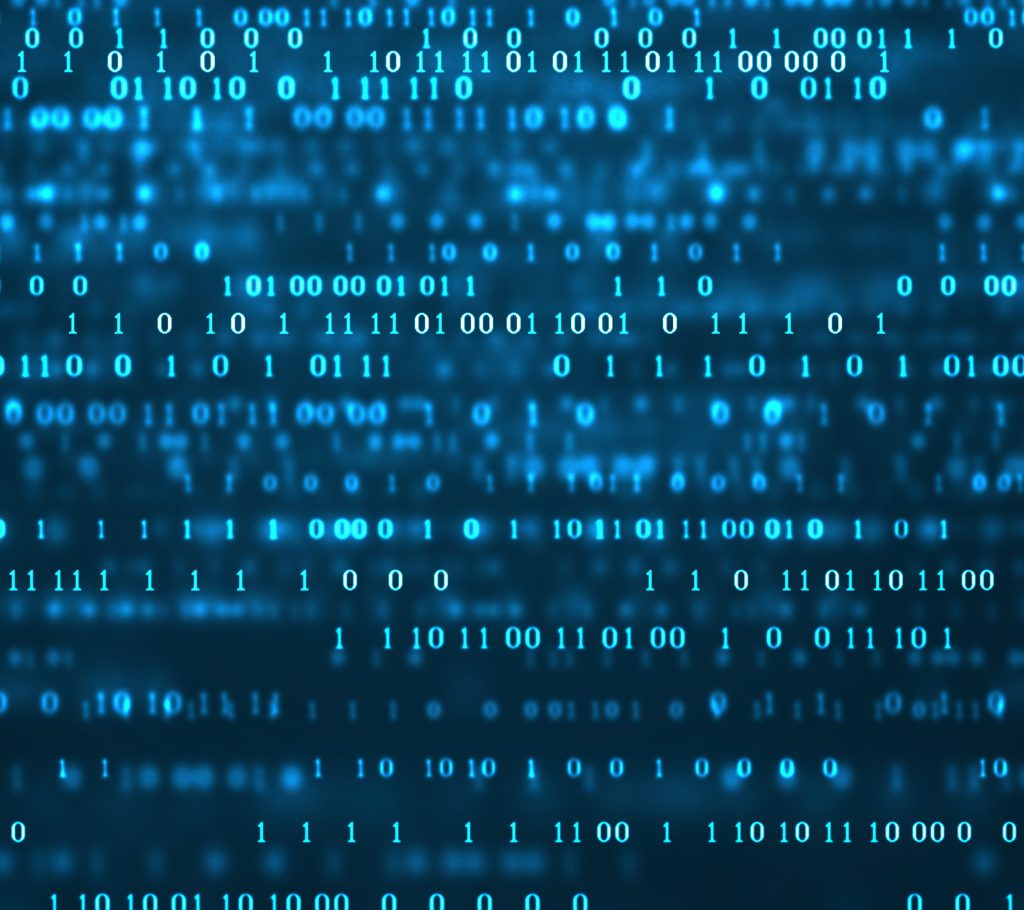
Focus your data insights on a specific goal
Have you given up yet? Too complex, too time-consuming, too technical, and too costly? You shouldn’t give up. What if there is a different way to access your data? One that starts from a business logic, a specific use case and a clear outcome that matters to you.
Example: Preventing equipment downtime
Let’s say your goal is to prevent unplanned asset downtime. It’s a specific challenge, the benefits to your company are clear and the data mountain has just become far smaller and specific.
So, what’s next?
- Define your specific goal. In our example, that could be 0 unplanned downtime due to overdue maintenance
- Identify the known key insights that could affect your goal
- List the data you need access to, and where it lives
- Design a workflow to implement a condition-based maintenance alert for a specific type of equipment
- Connect your data sources and add conditional rules
- Align with the operational teams involved and execute
- Monitor the result
- Plan timely maintenance
Cost and time savings are just a few of the benefits
This way of addressing the specific use case challenge – preventing equipment downtime – offers clear benefits:
- Early warning from a wide range of data sources that maintenance is required
- Automated actions to plan the maintenance
- Everyone knows what to do, including the many contractors on site
- No downtime, saving costs throughout your site and improving the efficiency of your operations
- New insights into your operations that may have been previously hidden through traditional data analysis
- Ability to scale this for other types of equipment and across all your sites